Who Else Wants Info About What Is The Preferred Method For Splicing Wires
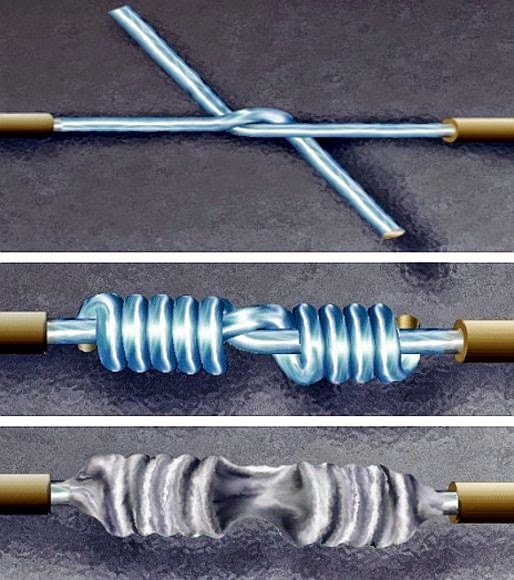
Splicing Wires
1. Why Does a Good Wire Splice Matter?
Alright, let's talk about splicing wires. It might not sound like the most glamorous topic, but trust me, a solid wire splice can be the difference between smooth sailing and a frustrating electrical problem. Think of it like this: a bad splice is like a weak link in a chain. It can cause resistance, overheating, flickering lights, and in extreme cases, even a fire. Nobody wants that! So, getting it right is pretty important, whether you're tackling a home improvement project or working on your car's wiring.
When you are making electrical connections, the goal is to create a bond that is as good as, or better than, the original wire. That means a connection that is mechanically sound and electrically conductive. A well-executed splice ensures that current flows smoothly and efficiently, without any hiccups. Its all about minimizing resistance, preventing corrosion, and making sure the connection holds up over time, even with vibrations and temperature changes. In short, a good splice is a reliable splice.
Before we dive into the "preferred" methods, let's quickly touch upon why we even splice wires in the first place. Sometimes, you need to extend a wire that's too short. Other times, you might be branching a circuit or repairing a damaged wire. Whatever the reason, a proper splice is crucial. There are many different ways to approach it, and the best method for you will depend on the specific situation and the tools you have available. We will explore a few of the most common and reliable techniques.
Think of selecting a splicing method like choosing the right tool for the job. You wouldn't use a hammer to screw in a screw, would you? Each method has its strengths and weaknesses, and knowing which one to use in different scenarios will make your electrical work safer and more effective. And that, my friends, is what we're aiming for: safe and effective connections that will last for years to come. No more flickering lights or unexplained circuit breaker trips!
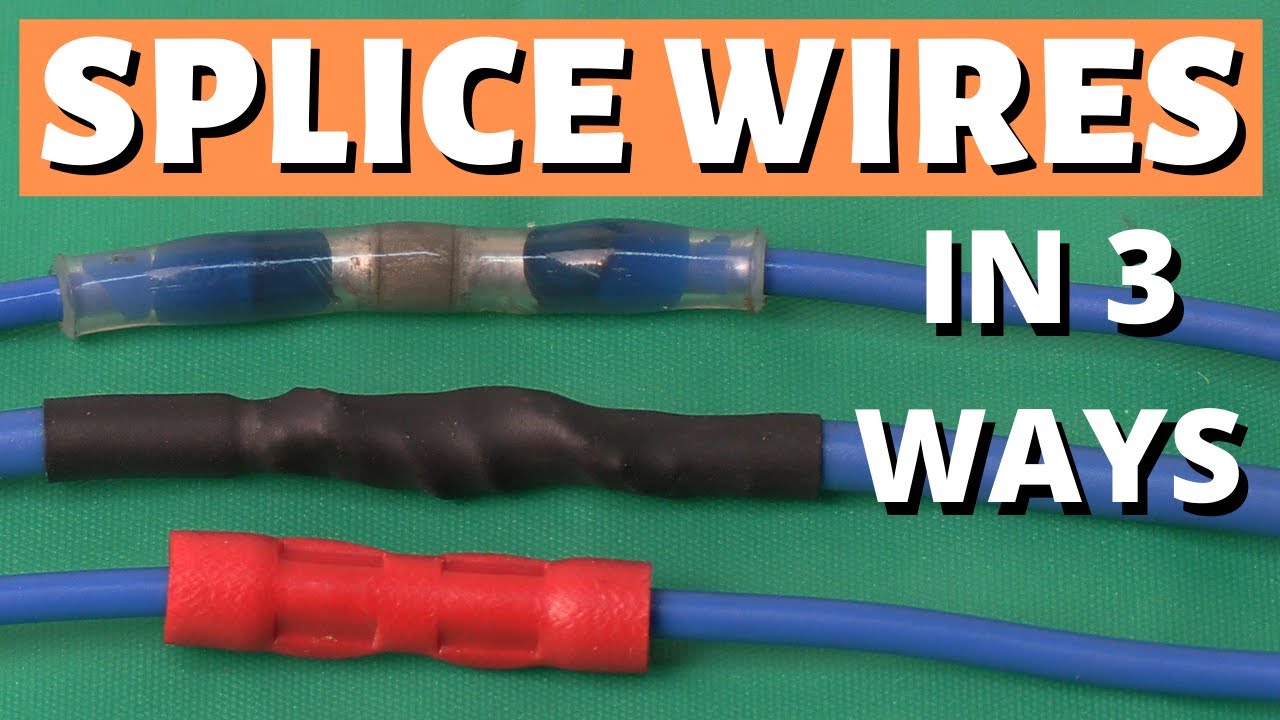
Splicing 3 Wires
Twist-On Wire Connectors (Wire Nuts)
2. The Old Reliable
Ah, wire nuts — those colorful little caps you often see poking out of electrical boxes. These are a staple for joining wires, especially in residential wiring. The process is straightforward: strip the ends of the wires, twist them together, and then screw on the wire nut. The twisting action creates a mechanical connection, and the wire nut keeps everything secure and insulated. Simple, right?
Now, here's the thing about wire nuts: they're super convenient and relatively inexpensive, but they're not always the absolute best choice for every situation. One potential drawback is that the connection relies on the tightness of the twist and the wire nut itself. Over time, vibration or temperature changes can loosen the connection, leading to problems. Plus, using the wrong size wire nut can cause issues. Too small, and it won't grip the wires properly; too large, and it might not create a tight enough connection.
To ensure a secure and reliable connection with wire nuts, there are a few best practices to follow. First, always use the correct size wire nut for the number and gauge of wires you are connecting. The packaging will provide a guide. Second, make sure the wires are stripped to the proper length, usually around 1/2 to 3/4 of an inch. Third, twist the wires together firmly before applying the wire nut. Some people even use pliers to give the twist an extra squeeze. Finally, give the wire nut a good tug after installation to make sure its securely holding the wires.
Despite their limitations, wire nuts remain a popular choice for many electricians and DIYers, and for good reason. They're quick, easy to use, and generally reliable when installed correctly. Plus, they're readily available at most hardware stores. So, while they may not be the ultimate splicing solution, they're definitely a solid option to have in your toolbox. Just remember to follow those best practices, and you'll be well on your way to a safe and secure electrical connection.

Crimp Connectors
3. Crimping for Keeps
Next up, we have crimp connectors. These bad boys offer a more permanent and arguably more reliable connection than wire nuts. With crimp connectors, you insert the stripped ends of the wires into the connector and then use a specialized crimping tool to compress the connector tightly around the wires. This creates a strong, gas-tight seal that's resistant to corrosion and vibration.
Crimp connectors come in various shapes and sizes, including butt connectors, ring terminals, and spade connectors. Butt connectors are commonly used for splicing wires together, while ring and spade connectors are often used to attach wires to screw terminals. The key to a good crimp is using the right connector for the wire gauge and using a quality crimping tool. A cheap crimper can damage the connector or not create a tight enough seal, leading to a faulty connection. The investment in a decent crimping tool is well worth it for the peace of mind it provides.
One of the biggest advantages of crimp connectors is their durability. Because the connection is so tight and secure, it's less likely to loosen over time, even in harsh environments. This makes them a great choice for automotive wiring, marine applications, and other situations where vibration and moisture are a concern. Another advantage is that they can often be used in tight spaces where it might be difficult to twist wires together. They offer a clean and professional look.
However, there are a few downsides to crimp connectors. First, they require a specialized tool, which can be an added expense. Second, once a crimp connector is installed, it's difficult to remove or reuse. If you need to make changes to the wiring, you'll likely have to cut the wire and install a new connector. Despite these drawbacks, crimp connectors are an excellent choice for creating strong, reliable, and long-lasting wire splices. When done correctly, a properly crimped connection is almost as strong as the wire itself.

Q What Is Proper Wire Splicing Anzer USA Blog
Soldering Wires
4. Soldering
Now we're getting serious. Soldering is considered by many to be the gold standard for wire splicing. It involves joining the wires together and then applying molten solder to create a permanent, electrically conductive bond. When done correctly, a soldered connection is incredibly strong, resistant to corrosion, and offers excellent electrical conductivity. It's the kind of connection that can last for decades.
The process of soldering involves a few key steps. First, the wires must be stripped and twisted together. Then, the connection is heated with a soldering iron, and solder is applied to the joint. The solder melts and flows into the gaps between the wires, creating a solid, conductive bridge. Once the solder cools, the connection is insulated with electrical tape or heat-shrink tubing. The quality of the solder is crucial for a good connection. Use rosin-core solder specifically designed for electrical work. Acid-core solder, often used in plumbing, is a big no-no for electrical applications.
Soldering offers several advantages. The main one is the superior electrical conductivity. Solder creates a very low-resistance connection, which means less energy loss and less heat buildup. Another advantage is the strength and durability of the connection. A properly soldered joint is highly resistant to vibration and corrosion, making it ideal for demanding environments. Plus, a soldered connection can be relatively small and compact, which is useful in tight spaces.
However, soldering is not without its challenges. It requires skill and practice to do well. Overheating the wires can damage them, and using too much solder can create a bulky, messy connection. It also takes more time than using wire nuts or crimp connectors. And of course, you need a soldering iron, solder, and safety gear like safety glasses. Finally, soldering can create fumes that are harmful to breathe, so it's important to work in a well-ventilated area. Despite these challenges, soldering remains a preferred method for many professionals and serious DIYers, especially when reliability and performance are paramount.
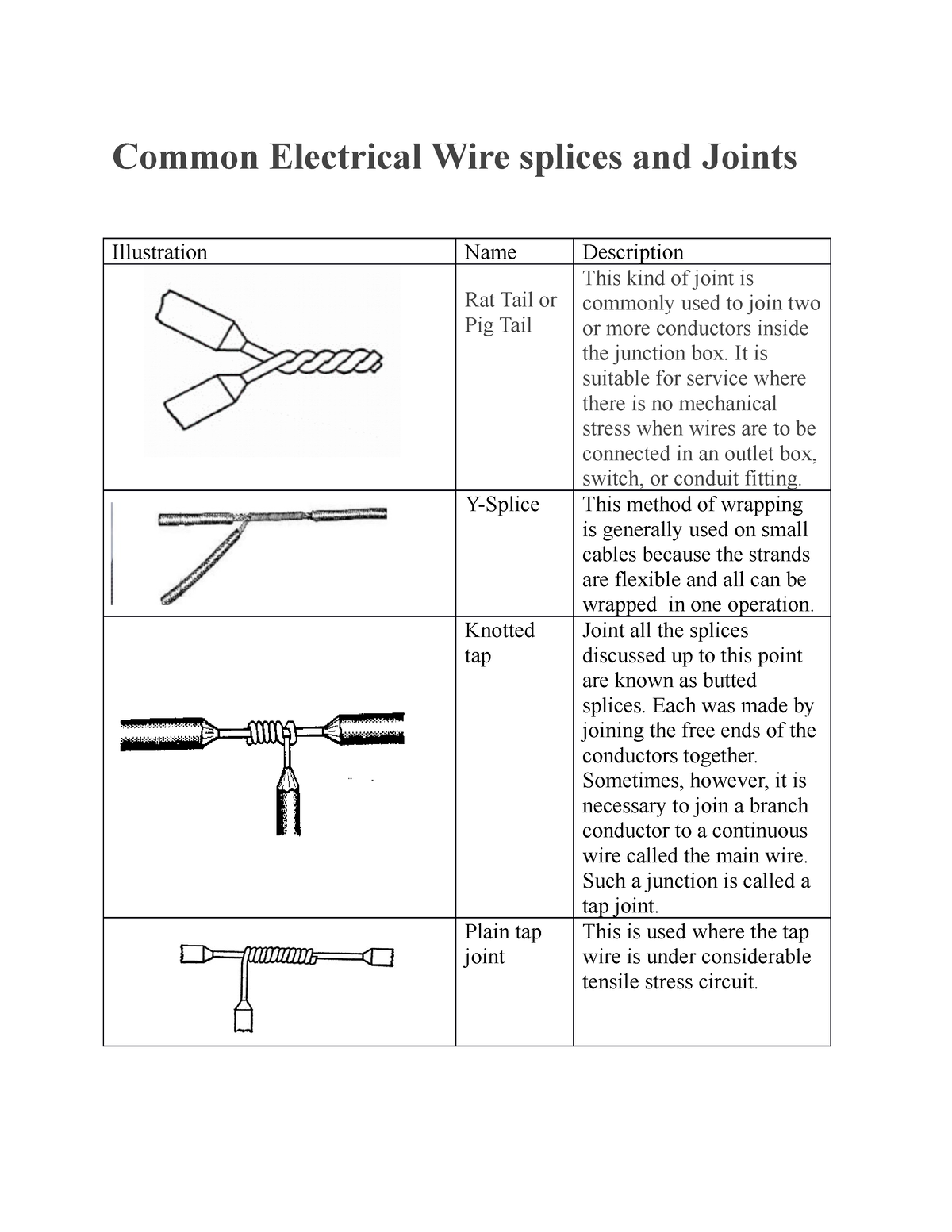
Electrical Wiring Splices Types Of Wire Joints
The Best Method
5. Choosing the Right Splicing Method for Your Needs
So, what is the preferred method for splicing wires? Well, as you've probably gathered by now, there's no one-size-fits-all answer. The best method depends on a variety of factors, including the type of wires, the environment, your skill level, and the tools you have available. Each method — wire nuts, crimp connectors, and soldering — has its pros and cons.
For simple residential wiring projects, wire nuts are often the go-to choice. They're easy to use, inexpensive, and generally reliable when installed correctly. Crimp connectors are a great option for automotive wiring, marine applications, and other situations where vibration and moisture are a concern. They offer a strong, durable, and corrosion-resistant connection. Soldering is the preferred method for critical applications where electrical conductivity and long-term reliability are paramount. It provides the strongest and most conductive connection, but it requires skill and patience.
Ultimately, the best way to determine the preferred method for your specific project is to consider the specific requirements and constraints. Are you working in a tight space? Do you need a connection that can withstand extreme temperatures or vibration? Are you comfortable with soldering, or would you prefer a simpler method? Answering these questions will help you narrow down your options and choose the method that's best suited to your needs.
No matter which method you choose, always remember to prioritize safety. Turn off the power before working on any electrical circuits, and use appropriate safety gear, such as safety glasses and gloves. Also, follow the manufacturer's instructions for any tools or connectors you're using. With a little bit of knowledge and careful attention to detail, you can create safe and reliable wire splices that will last for years to come. And that, my friends, is the ultimate goal.

Diffe Types Of Wire Splices Wiring Draw
FAQ
6. Your Wire Splicing Questions, Answered!
Let's tackle some common questions about splicing wires. Hopefully, this will clear up any lingering doubts and give you the confidence to tackle your next wiring project.
Q: Can I mix different gauges of wire in a splice?
A: Generally, it's best to avoid mixing significantly different wire gauges. If you must, ensure the connection is rated for the lower gauge wire, and use a connector appropriate for the combination. For instance, use a wire nut rated for the thinner wire.
Q: Is it safe to splice wires outside?
A: Splicing wires outside requires extra precautions to protect the connection from moisture. Use waterproof connectors or weatherproof enclosures. Always ensure the connection is rated for outdoor use.
Q: What's the best way to insulate a wire splice?
A: Electrical tape is a common option, but heat-shrink tubing provides a more durable and waterproof seal. Ensure the insulation covers the entire exposed wire and extends slightly onto the existing insulation.
Q: Can I reuse wire nuts?
A: It's generally not recommended to reuse wire nuts. Over time, they can lose their grip and become less reliable. It's always best to use new wire nuts for each connection.